Multifunction controller – processes automated, energy saved
Cost-effective, versatile and easy-to-use controller from HESCH replaces PLCs
An innovative multifunction controller (MFC) easily takes over the automation of applications for which a programmable logic controller (PLC) is oversized: HESCH Industrie-Elektronik GmbH, specializing in industrial automation solutions, eliminates the need for a costly PLC in many cases with its easy-to-use controller. An example from the food industry demonstrates how companies can use it to achieve more efficient and energy-saving processes.
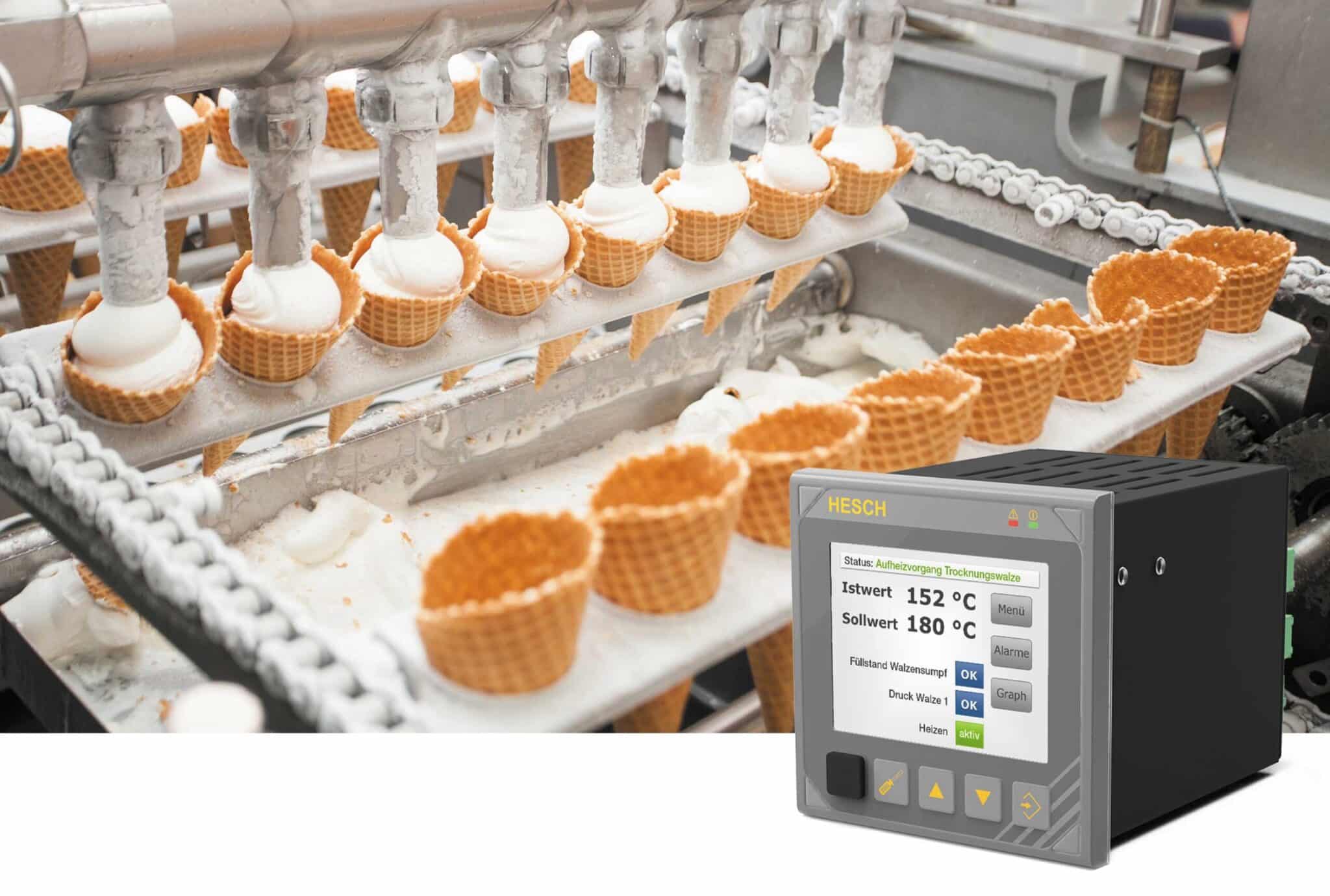
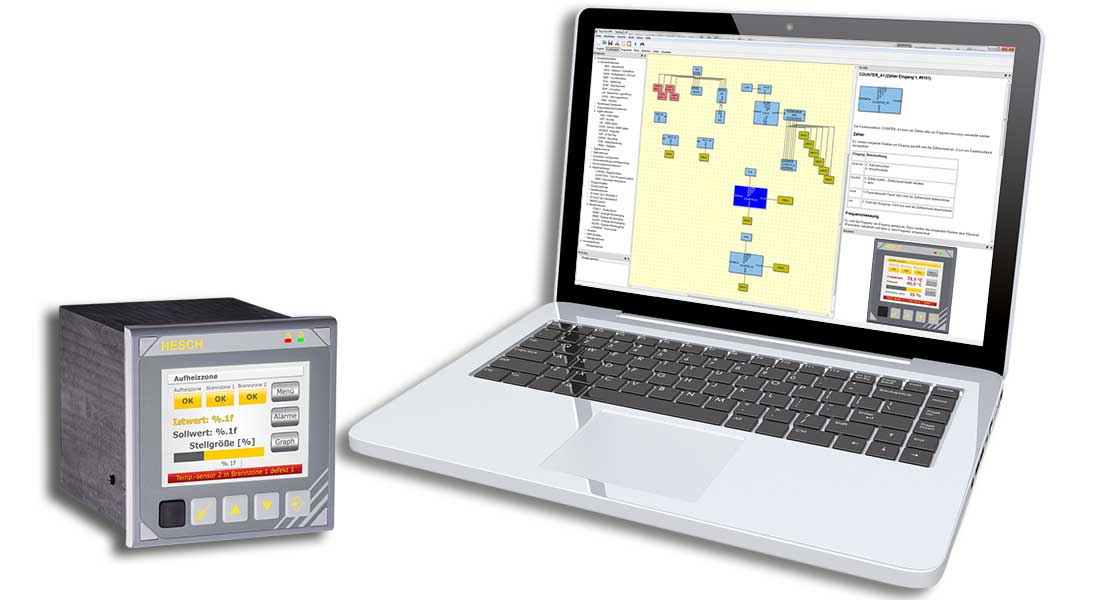
With automation, production processes achieve greater efficiency. For example, energy costs can be reduced by controlled heating processes of production plants. HESCH has developed the multifunction controller (HE 5697 MFC) for automated sequence control including the control of further auxiliary processes. It is characterized by simple handling, can be set up even without in-depth programming knowledge and allows an individual design of the user interface.
Its outstanding advantage: In many cases, the controller makes the investment in a cost-intensive PLC unnecessary.
Automation with MFC – a win in every respect
Among others, a company from the food industry achieved decisive improvements in production by using the MFC. For the automation of a roller drying plant for the production of the additive casein – a milk protein that is indispensable for the manufacture of a wide variety of products – the manufacturer was looking for an easy-to-operate control system.
With the MFC from HESCH, a single controller now takes over sequence control as well as the control of other secondary processes: It monitors the surface temperature of the roll as well as the strength of the steam pressure – a process previously controlled manually. In addition, the MFC controls the pump for product conveying in conjunction with the level measurement.
The MFC offers various communication possibilities via Profinet Class A, Profibus DP Slave, Modbus RTU Master, Modbus RTU Slave, Modbus TCP Client, Modbus TCP Server, Can Bus, or HPR Bus Master.
The casein manufacturer benefits from the automated processes in several ways. The process is becoming more efficient and energy-saving overall. For example, heating the rollers to operating temperature now takes only 3.5 hours instead of 8 to 12 hours. This significantly saves energy for the food additive manufacturer. Precise control of the parameters also ensures consistent product quality. In addition, the yield has increased significantly, as burning of the products is prevented by the precise temperature control. At the same time, this reduces wear on the knives and thus lowers the maintenance costs of the plant. In addition, the manufacturer is creating new capacities: Employees who were used for manual process control can now take over other activities.
“In many cases, a costly programmable logic controller (PLC) used to automate simple applications provides many functions that are superfluous. In addition, their use usually requires in-depth programming knowledge. In these cases, our MFC offers a cost-effective solution that can be used to make significant savings in times of high energy costs, among other things,” explains Werner Brandis, Managing Director at HESCH.